From Industrial Robots to Collaborative Robots: A New Era of Automation
Imagine a factory floor where humans and robots work side by side, harmoniously assembling products with precision and efficiency. This scenario, once a distant vision, is now a reality thanks to the evolution from traditional industrial robots to collaborative robots, or "cobots." This shift marks a new era in automation, transforming industries and redefining the roles of human workers.
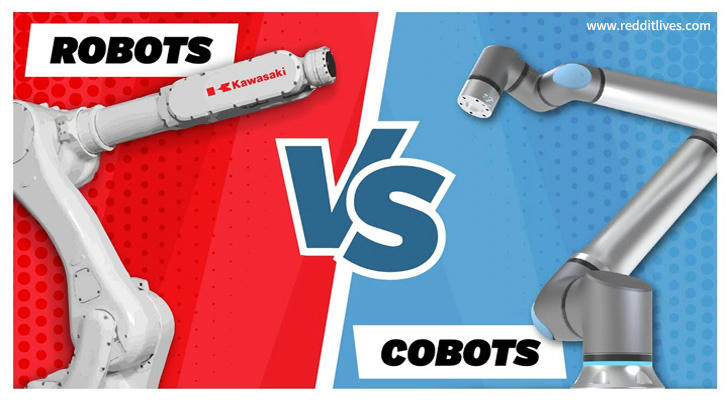
The Rise of Industrial Robots
Industrial robots have been the backbone of manufacturing automation for decades. These machines are typically larger, faster, and more powerful than cobots, with a higher payload capacity and greater range of motion. They are often enclosed in safety cages or barriers to protect human workers from potential harm. Common applications of industrial robots include welding, painting, material handling, and packaging.
While these robots excel at performing repetitive tasks with high precision and speed, their operation requires significant investment in safety infrastructure and specialized programming. This has traditionally limited their use to large-scale manufacturing environments where high-volume production justifies the costs. For example, the global market for industrial robots was valued at $16.8 billion in 2020, with the automotive and electronics industries accounting for over 60% of installations (International Federation of Robotics, 2021).
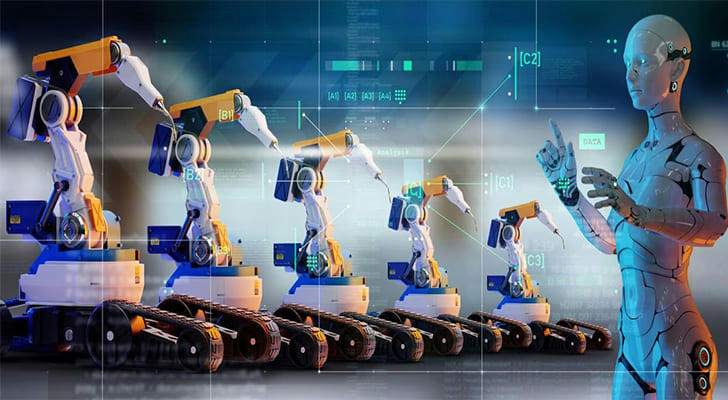
The Emergence of Collaborative Robots
In contrast, collaborative robots, or cobots, are designed to work alongside human operators in a shared workspace. This capability opens up new possibilities for collaborative manufacturing environments, where robots and humans can collaborate on tasks in real-time.
Collaborative robots are equipped with advanced sensors and safety features that allow them to detect the presence of humans and operate without the need for extensive safety barriers. This design not only reduces the physical footprint of the automation system, but also lowers the initial investment required, making automation accessible to businesses of all sizes. According to a report by MarketsandMarkets, the global collaborative robots market is expected to grow from $1.2 billion in 2022 to $8.3 billion in 2027, at a compound annual growth rate (CAGR) of 43.4%.
Advantages of Cobots Over Traditional Industrial Robots
1.Safety and Collaboration: Cobots are inherently safe for human-robot collaboration. They have sensors that help them detect when a person is nearby, allowing them to slow down or stop to avoid accidents. For instance, cobots from Universal Robots are equipped with force-limiting technology, ensuring they stop immediately upon contact with a human.
2.Flexibility and Ease of Use: Cobots are designed to be user-friendly and easily programmable, allowing operators without extensive technical expertise to set up and reprogram tasks. For example, Universal Robots' cobots can be programmed using intuitive drag-and-drop software, reducing setup time by up to 80% compared to traditional robots.
3.Cost-Effectiveness: Cobots have a lower purchase price, maintenance costs, and energy consumption, with an average ROI of one year. A study by the International Federation of Robotics found that SMEs adopting cobots reported a 30% reduction in production costs within the first year of implementation.
4.Mobility and Space Efficiency: Cobots are considerably easier to install and operate than traditional robots. Their compact design allows them to work in confined spaces, reducing the need for infrastructure modifications. For example, cobots like the UR3e from Universal Robots weigh just 24.3 pounds, making them highly portable and adaptable to various workspaces.
Applications of Collaborative Robots
The versatility of cobots has led to their adoption across various industries and applications:
•Assembly: Automotive giant BMW uses cobots on production lines to assist workers in assembling car parts, reducing fatigue and increasing efficiency. In one case, cobots helped BMW achieve a 15% increase in productivity on a specific assembly line.
•Machine Tending: Small manufacturing firms, like CNC machining companies, deploy cobots to load and unload machines, freeing human workers for quality control tasks. A study by the Association for Advancing Automation found that cobots reduced machine idle time by 20% in small-scale manufacturing setups.
•Material Handling: Amazon has integrated cobots into its warehouses to assist in sorting and transporting packages, significantly improving order fulfillment speed. The company reported a 40% reduction in order processing time after deploying cobots in its logistics centers.
•Quality Inspection: Electronics manufacturers employ cobots equipped with AI-powered vision systems to detect defects in circuit boards with high precision. For instance, a leading electronics manufacturer reported a 25% improvement in defect detection rates after implementing cobots.
•Welding: Boeing has adopted cobots for precise welding in aircraft production, reducing human exposure to hazardous environments. The use of cobots in welding operations has led to a 30% reduction in rework rates due to improved precision.
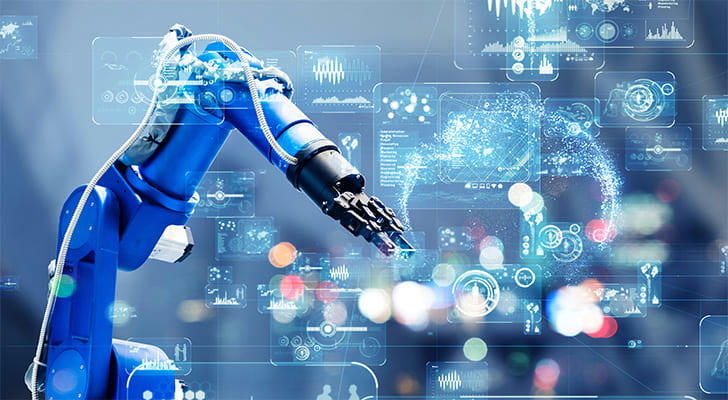
Challenges and Considerations
Despite their advantages, the integration of cobots into existing workflows presents challenges:
•Speed and Precision: While cobots are designed for safety and flexibility, they may not match the speed and precision of traditional industrial robots in high-volume production environments. For example, cobots typically operate at speeds of 1-4 meters per second, compared to industrial robots that can reach speeds of up to 10 meters per second.
•Human Resources: The successful deployment of cobots requires personnel with appropriate expertise. While cobots are generally more user-friendly than traditional robots, a lack of sufficient knowledge about their capabilities and limitations can hinder effective integration. A survey by Deloitte found that 45% of SMEs cited a lack of skilled workers as a barrier to adopting cobot technology.
The Future of Automation
The transition from industrial robots to collaborative robots signifies a broader trend toward more adaptable, human-centric automation solutions. As technology advances, we can expect cobots to become even more capable, handling complex tasks and further integrating into various aspects of production and service industries.
For example, medical cobots are being used in hospitals for surgical assistance, such as the da Vinci Surgical System, which enables precise, minimally invasive procedures. Similarly, the food industry is leveraging cobots for automated food preparation, reducing contamination risks.
This evolution not only enhances operational efficiency but also empowers human workers to engage in more meaningful, less hazardous work, fostering a more innovative and productive industrial landscape.
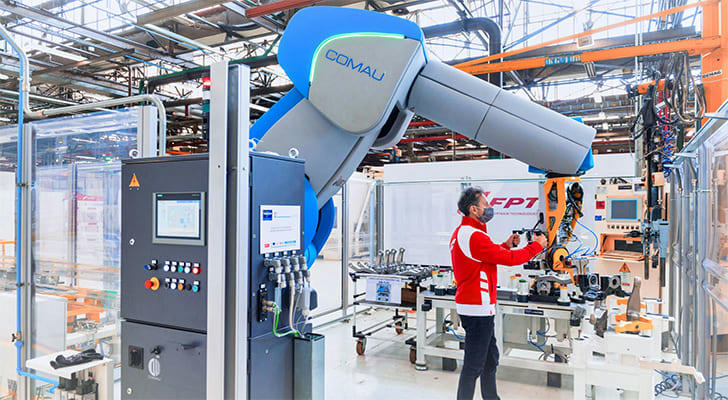
Conclusion
The advent of collaborative robots marks a pivotal shift in automation, offering safer, more flexible, and cost-effective solutions compared to traditional industrial robots. As industries continue to embrace this technology, the synergy between human ingenuity and robotic precision will undoubtedly drive the next wave of industrial innovation.
By bridging the gap between humans and machines, cobots are not just tools but partners in progress, paving the way for a future where automation is more inclusive, adaptable, and transformative than ever before.